A metal cutting band saw is a powerful and versatile machine tool used for cutting various types of metals, including ferrous and non-ferrous materials. It is characterized by its continuous band-shaped blade that rotates around two or more wheels, providing a smooth and efficient cutting action.
Metal cutting band saws can be classified into two main types: horizontal and vertical. Horizontal band saws are typically used for cutting larger workpieces, such as structural beams, pipes, or bars, while vertical band saws are better suited for cutting smaller components or intricate shapes.
The main components of a metal cutting band saw include:
- Band Saw Blade: This is the cutting tool, made of high-quality steel or bi-metal materials, designed to withstand the rigors of cutting through tough metals. Band saw blades come in various sizes, tooth configurations, and materials to suit different applications.
- Drive Wheels: These are the large wheels that rotate and drive the band saw blade. They are typically made of cast iron or aluminum and are precisely machined to ensure smooth blade tracking and minimize vibrations.
- Blade Guides: These components support and guide the band saw blade, ensuring accurate and straight cuts. They are adjustable to accommodate different blade sizes and minimize blade deflection during cutting.
- Coolant System: Many metal cutting band saws are equipped with a coolant system that sprays a coolant mixture onto the blade and workpiece during cutting. This helps to reduce heat buildup, extend blade life, and improve cutting performance.
- Feed Mechanism: Depending on the type of band saw, the feed mechanism can be manual, hydraulic, or computer-controlled. It controls the rate at which the workpiece is fed into the blade, allowing for precise and consistent cuts.
Metal cutting band saws are widely used in various industries, including metalworking, fabrication, construction, and automotive, due to their ability to make accurate and efficient cuts on a wide range of materials.
Table of Contents
Applications and Industries
Metal cutting band saws are versatile tools used across a wide range of industries for cutting various materials, including metals, plastics, and composites. Their ability to make accurate cuts with minimal material waste makes them essential in manufacturing, construction, metalworking, and other sectors.
Manufacturing: Band saws are commonly used in manufacturing facilities for cutting stock materials, such as bars, tubes, and structural shapes, into desired lengths or shapes. They are particularly useful in the production of automotive parts, appliances, machinery components, and other metal fabrication applications.
Construction: In the construction industry, band saws are employed for cutting structural steel, rebar, and other metal components used in building structures. Their portability and ability to make precise cuts on-site make them invaluable tools for contractors and ironworkers.
Metalworking: Metal cutting band saws are indispensable in metalworking shops, fabrication facilities, and machine shops. They are used for cutting various metal materials, including steel, aluminum, brass, and stainless steel, into desired shapes and sizes for further processing or assembly.
Woodworking: While primarily designed for metal cutting, some band saws can also be used for cutting wood, particularly in woodworking shops and furniture manufacturing. They are capable of making intricate cuts and patterns in wood, making them useful for creating custom designs and shapes.
Recycling and Scrap Metal Processing: Band saws play a crucial role in the recycling industry, where they are used to cut and process scrap metal, such as old machinery, vehicles, and other metal objects, into smaller pieces for easier handling and transportation.
Shipbuilding and Repair: In the shipbuilding and repair industry, large-scale band saws are employed for cutting thick metal plates, beams, and other structural components used in the construction and repair of ships and offshore structures.
Overall, metal cutting band saws are versatile tools that find applications in various industries where precise cutting of metals, plastics, and other materials is required. Their ability to make clean, accurate cuts with minimal material waste makes them invaluable in manufacturing, construction, metalworking, and many other sectors.
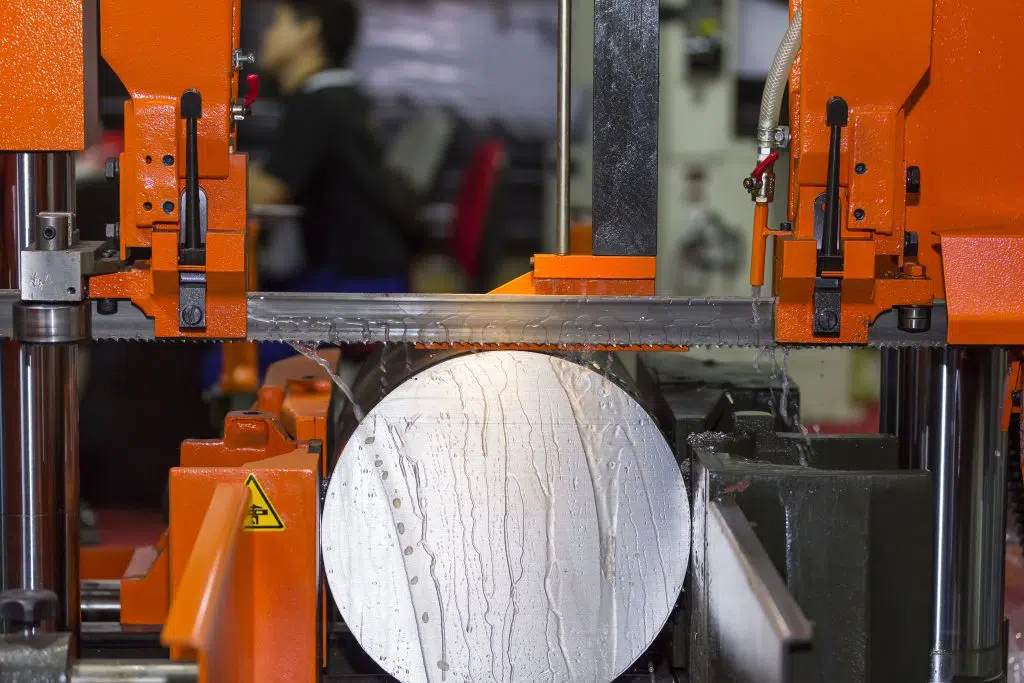
How Does a Band Saw Work?
A band saw operates on a simple yet effective principle: a continuous metal blade rotates around two wheels, with the cutting action occurring on the downward-moving section of the blade. The blade is tensioned to maintain its shape and prevent deflection during the cutting process.
The cutting mechanism of a band saw relies on the blade’s teeth, which are carefully designed to efficiently remove material. As the blade rotates, the teeth make successive cuts, gradually slicing through the workpiece. The blade’s motion is typically vertical, allowing for straight or contoured cuts, depending on the operator’s guidance.
The blade motion is driven by an electric motor that powers one of the wheels, causing the blade to rotate continuously. The motor’s power and the blade’s speed are adjustable, allowing for optimal cutting performance based on the material and the desired cut quality.
During operation, the workpiece is securely clamped or supported on the saw’s table, which can be adjusted to accommodate different workpiece sizes and angles. The operator then guides the workpiece into the downward-moving section of the blade, controlling the feed rate and direction to achieve the desired cut.
Band saws are particularly efficient for curved or irregular cuts, as the narrow blade can negotiate tight radii and intricate shapes with relative ease. The continuous blade design also minimizes the risk of binding or kickback, enhancing safety during operation.
Band Saw Blades
Band saw blades come in various types, materials, and tooth configurations, each designed for specific cutting applications and materials. Understanding the different blade options is crucial for achieving optimal performance and prolonged blade life.
Types of Blades:
- All-Purpose Blades: These versatile blades are suitable for cutting a wide range of materials, including mild steel, aluminum, and plastic. They feature a general-purpose tooth pattern and are a good choice for various cutting tasks.
- Metal-Cutting Blades: Designed specifically for cutting ferrous and non-ferrous metals, these blades have teeth optimized for metal cutting. They are available in different tooth configurations, such as regular, raker, and variable-pitch teeth, depending on the metal type and thickness.
- Wood-Cutting Blades: With a distinct tooth pattern and set, wood-cutting blades are optimized for cutting various wood materials, including hardwoods and softwoods. They provide smooth and accurate cuts while minimizing tear-out.
- Bi-Metal Blades: These blades feature a combination of a flexible backing material and a harder tooth edge material, such as high-speed steel or carbide. Bi-metal blades offer superior wear resistance and longer blade life, making them suitable for cutting abrasive materials or high-volume production environments.
Blade Materials:
- Carbon Steel: A common and economical choice for general-purpose applications, carbon steel blades are suitable for cutting mild steel, aluminum, and plastics.
- High-Speed Steel (HSS): HSS blades are harder and more wear-resistant than carbon steel, making them suitable for cutting harder materials like stainless steel and tool steels.
- Carbide-Tipped: Blades with carbide-tipped teeth offer exceptional hardness and wear resistance, ideal for cutting abrasive materials or high-volume production environments.
Tooth Configurations:
- Regular Tooth: A standard tooth pattern with evenly spaced teeth, suitable for general-purpose cutting.
- Raker Tooth: Featuring a tooth pattern with alternating tall and short teeth, raker tooth blades are designed for efficient chip removal and cutting harder materials.
- Variable-Pitch Tooth: With teeth spaced at varying intervals, variable-pitch tooth blades reduce vibration and noise, making them suitable for cutting thin-walled or bundles of materials.
Blade Selection:
Selecting the appropriate blade is essential for achieving optimal cutting performance and blade life. Consider factors such as the material being cut, thickness, production volume, and desired surface finish. Consulting blade manufacturer recommendations or seeking advice from experienced professionals can help ensure the right blade choice for your specific application.
Choosing the Right Band Saw
Selecting the right metal cutting band saw for your needs is crucial to ensure efficient and precise cutting operations. Several factors should be considered when choosing a band saw, including size, power, speed, capacity, and features.
Size: Band saws come in various sizes, ranging from compact benchtop models to large floor-standing machines. The size you choose will depend on the workspace available, the size of the materials you plan to cut, and the portability requirements. Smaller saws are more compact and easier to move, while larger saws offer greater cutting capacity and stability.
Power: The power of a band saw is typically measured in horsepower (HP) or watts. More powerful saws can handle thicker and harder materials with ease, but they also consume more energy and generate more noise. Consider the types of materials you’ll be cutting and their thickness to determine the appropriate power level.
Speed: Band saws operate at different blade speeds, measured in feet per minute (FPM) or meters per minute (MPM). Slower speeds are suitable for cutting softer materials, while faster speeds are better for harder materials. Some saws offer variable speed control, allowing you to adjust the blade speed according to the material being cut.
Capacity: The cutting capacity of a band saw refers to the maximum dimensions of the material it can accommodate. This is typically defined by the throat depth (the distance from the blade to the column) and the maximum cutting height. Ensure that the saw you choose can handle the largest workpieces you anticipate cutting.
Features: Band saws can come equipped with various features that enhance their functionality and ease of use. Some common features include:
- Blade guides: Adjustable blade guides help keep the blade stable and reduce deflection, resulting in straighter cuts.
- Miter gauge: A miter gauge allows you to make angled cuts with precision.
- Coolant system: A coolant system helps keep the blade and workpiece cool during cutting, extending blade life and improving cut quality.
- Automatic shutoff: This feature automatically stops the saw when the cut is complete, improving safety and reducing wear.
- Blade tension adjustment: Proper blade tension is essential for accurate cuts and longer blade life. Look for saws with easy-to-adjust blade tension mechanisms.
By carefully considering these factors, you can select a metal cutting band saw that meets your specific requirements, ensuring efficient and accurate cutting operations while maximizing productivity and safety.
Setting Up and Operating a Band Saw
Proper setup and operation of a metal cutting band saw is crucial for ensuring accurate cuts, prolonging the lifespan of the machine, and maintaining a safe working environment. Here are the key steps to follow:
Installation
Most band saws come partially assembled, but you’ll need to mount the saw on a sturdy workbench or stand. Follow the manufacturer’s instructions carefully, ensuring that the saw is level and securely fastened to prevent vibrations or movement during operation.
Adjustments
Before starting any cutting operation, it’s essential to make the necessary adjustments to the band saw:
- Blade Tracking: Ensure that the blade is running straight and centered on the wheels. Improper tracking can cause premature blade wear and inaccurate cuts.
- Blade Tension: Adjust the blade tension according to the manufacturer’s specifications for the blade size and material being cut. Overtensioning can cause blade breakage, while undertensioning can lead to blade deflection and inaccurate cuts.
- Blade Guides: Adjust the blade guides to provide minimal clearance around the blade, preventing excessive blade deflection while allowing smooth movement.
Safety Precautions
Metal cutting band saws can be dangerous if not operated correctly. Always follow these safety guidelines:
- Wear appropriate personal protective equipment (PPE), including safety glasses, gloves, and hearing protection.
- Keep the work area clean and free from clutter, ensuring a clear path around the saw.
- Never wear loose clothing or jewelry that could get caught in the moving parts.
- Ensure that the saw is properly grounded and that all guards and safety mechanisms are in place and functioning correctly.
Cutting Techniques
When operating a metal cutting band saw, follow these techniques for optimal results:
- Workpiece Preparation: Secure the workpiece firmly in a vise or clamp to prevent movement during cutting.
- Feed Rate: Apply a steady, consistent feed rate, allowing the blade to cut smoothly without forcing it. Excessive feed rates can cause blade breakage or inaccurate cuts.
- Coolant: Use a coolant or lubricant recommended for the material being cut to prolong blade life and improve cutting efficiency.
- Blade Selection: Choose the appropriate blade for the material, thickness, and type of cut required. Consult the manufacturer’s recommendations or seek advice from experienced operators.
By following these guidelines for setting up and operating a metal cutting band saw, you can ensure accurate cuts, maximize the lifespan of your equipment, and maintain a safe working environment.
Maintenance and Troubleshooting
Proper maintenance and troubleshooting are essential for ensuring the longevity and optimal performance of your metal cutting band saw. Regular maintenance can help prevent costly breakdowns and extend the lifespan of your equipment.
Blade Tracking and Tension
Maintaining the correct blade tracking and tension is crucial for achieving accurate cuts and preventing premature blade wear or breakage. Improper blade tracking can cause the blade to wander or drift, leading to uneven or inaccurate cuts. Insufficient tension can cause the blade to deflect or vibrate excessively, while excessive tension can lead to premature blade fatigue and breakage.
To ensure proper blade tracking, regularly inspect the blade guides and adjust them as necessary. The blade should run smoothly through the guides without excessive friction or binding. Additionally, check the blade tension according to the manufacturer’s recommendations and adjust it as needed.
Cleaning and Lubrication
Regular cleaning and lubrication of the band saw’s components are essential for maintaining smooth operation and preventing premature wear. Accumulated debris, such as metal chips or dust, can cause friction and wear on moving parts, leading to premature failure.
Clean the machine regularly, using a brush or compressed air to remove debris from the blade guides, pulleys, and other exposed areas. Lubricate the blade guides, bearings, and other moving parts according to the manufacturer’s instructions, using the recommended lubricants.
Common Issues and Troubleshooting
Even with proper maintenance, band saws can experience issues that require troubleshooting. Some common problems and their potential solutions include:
- Blade Wandering or Drifting: This can be caused by improper blade tracking, worn or misaligned blade guides, or a dull or damaged blade. Adjust the blade guides, check the blade tension, and replace the blade if necessary.
- Excessive Vibration: Vibration can be caused by a dull or damaged blade, improper blade tension, or worn bearings or pulleys. Replace the blade, adjust the tension, or replace worn components as needed.
- Blade Breakage: Blade breakage can result from excessive tension, improper blade selection for the material being cut, or cutting into hard objects or foreign materials. Ensure proper blade selection and tension, and inspect the workpiece for potential hazards.
- Motor or Drive Issues: Problems with the motor or drive system can lead to reduced cutting performance or complete failure. Check for worn belts or chains, lubricate bearings, and inspect the motor and electrical components for any issues.
Regular maintenance, proper setup, and prompt troubleshooting can help ensure your metal cutting band saw operates efficiently and reliably, providing accurate and consistent cuts for years to come.
Safety Considerations
Proper safety precautions are crucial when operating a metal cutting band saw to prevent serious injuries. Wearing appropriate personal protective equipment (PPE) is essential. This includes safety glasses or a face shield to protect your eyes from flying debris, cut-resistant gloves to protect your hands, and hearing protection to safeguard your ears from the loud noise generated by the saw.
Guarding is another critical safety feature on band saws. The blade should be enclosed by a adjustable guard that covers as much of the blade as possible while still allowing the workpiece to pass through. Never remove or bypass these guards, as they are designed to prevent accidental contact with the blade.
When handling materials, be cautious of sharp edges and burrs that can cause cuts or scratches. Use appropriate lifting techniques or material handling equipment to avoid strains or injuries from heavy workpieces. Ensure that the workpiece is securely clamped or supported before cutting to prevent it from shifting or binding during the cut.
Proper workspace setup is also important for safe operation. Keep the area around the band saw clear of clutter, tools, and debris that could cause tripping hazards or obstruct movement. Ensure adequate lighting and ventilation to maintain visibility and reduce exposure to dust and fumes. Never operate the band saw while under the influence of drugs, alcohol, or medication that could impair your judgment or reflexes.
Accessories and Attachments
Accessories and attachments can greatly enhance the functionality and efficiency of a metal cutting band saw. Some common accessories include:
Workstands: Workstands or roller stands are designed to support long or heavy workpieces, allowing for easier and more precise cutting. They can be adjusted to different heights and angles, providing better stability and reducing operator fatigue.
Guides: Band saw guides help keep the blade running straight and true, minimizing blade deflection and ensuring accurate cuts. They are available in different materials, such as ceramic or metal, and can be adjusted to accommodate different blade widths.
Coolant Systems: Cutting through metals generates significant heat, which can cause premature blade wear and workpiece deformation. Coolant systems, either flood or mist, help dissipate heat and extend blade life by continuously applying a coolant or lubricant to the cutting area.
Dust Collection: Metal cutting band saws can produce a significant amount of chips and dust, which can create a hazardous working environment. Dust collection systems, either built-in or external, help capture and remove these particles, improving visibility and maintaining a clean workspace.
Other accessories may include blade brushes for cleaning the blade, chip brushes for clearing away chips and debris, and various clamping devices for securely holding workpieces in place during cutting operations.
Popular Brands and Models
When it comes to metal cutting band saws, there are several reputable brands and models to consider. Each manufacturer offers a range of options with varying features, capacities, and price points to suit different industrial and commercial needs.
One of the leading brands in the market is DoAll, known for their robust and durable band saws. The DoAll Dual Mist Band Saw series, for instance, is designed for high-performance cutting and features a unique mist lubrication system for improved blade life and cutting efficiency. Another popular option from DoAll is the DV-20 Vertical Band Saw, which offers a compact footprint and versatile cutting capabilities.
Jet is another well-respected brand in the metal cutting industry, offering a wide range of band saws for various applications. The Jet HVBS-712K Horizontal/Vertical Band Saw is a versatile machine that can handle both horizontal and vertical cutting operations, making it a popular choice for workshops and small-scale production facilities.
Grizzly is a brand known for its affordable yet reliable band saws. The Grizzly G0561 Horizontal Band Saw is a budget-friendly option that delivers solid performance and accuracy for light to medium-duty cutting tasks.
For heavy-duty industrial applications, brands like Marvel and Hydmech are worth considering. Marvel’s Horizontal Band Saws are designed for high-volume production environments, offering robust construction and powerful cutting capabilities. Hydmech’s Vertical Band Saws, on the other hand, are renowned for their precision and efficiency in cutting large workpieces.
When comparing different models, it’s essential to consider factors such as cutting capacity, blade speed, material handling capabilities, and overall build quality. Some models may offer additional features like automatic blade tensioning, coolant systems, or programmable controls for enhanced productivity and ease of use.
Ultimately, the choice of brand and model will depend on the specific requirements of the application, budget constraints, and the user’s preferences for features and performance. It’s always advisable to research and compare various options to find the best fit for your metal cutting needs.