A torque wrench is a specialized tool designed to apply and measure a precise amount of rotational force, or torque, to a fastener, such as a nut or bolt. It is an essential tool in many industries, including automotive, aerospace, construction, and manufacturing, where proper tightening of fasteners is crucial for safety, performance, and reliability.
The primary purpose of a torque wrench is to ensure that fasteners are tightened to the manufacturer’s specified torque value, preventing under-tightening or over-tightening. Under-tightening can lead to loosening and potential failure, while over-tightening can cause damage to the fastener or the components being assembled.
The basic working principle of a torque wrench involves a calibrated mechanism that measures the torque applied to the fastener. As the user applies force to the handle, the wrench’s internal mechanism engages and measures the torque. When the desired torque value is reached, the wrench will typically provide a audible or tactile signal, such as a click or a release of tension, indicating that the correct torque has been achieved.
Table of Contents
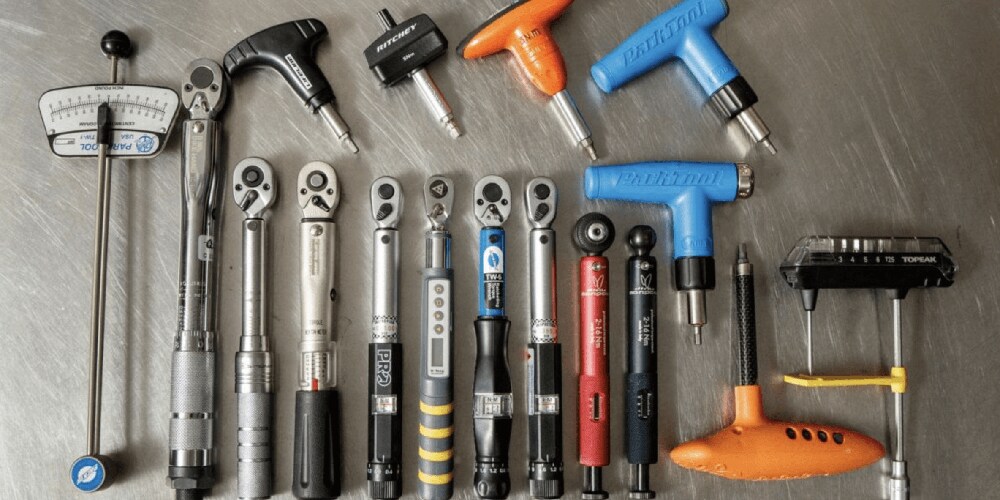
Types of Torque Wrenches
Torque wrenches come in various types, each with its unique features and advantages. Here are the most common types:
Beam-Type Torque Wrench: This is one of the oldest and most recognizable types of torque wrenches. It features a long beam with a pointer that moves along a scale, indicating the applied torque. Beam-type torque wrenches are known for their simplicity, durability, and ease of use. They are often preferred for their visual feedback and ability to hold the set torque value.
Dial-Type Torque Wrench: Dial-type torque wrenches use a dial or gauge to display the applied torque value. They are more compact and easier to use in tight spaces compared to beam-type wrenches. Dial-type wrenches offer accurate readings and are often preferred for their precision and ease of use.
Click-Type Torque Wrench: Also known as a micrometer torque wrench, this type features a mechanism that produces an audible “click” sound when the desired torque value is reached. Click-type torque wrenches are popular for their convenience and ability to provide a clear indication when the target torque is achieved.
Electronic Torque Wrench: As the name suggests, electronic torque wrenches use electronic sensors and a digital display to measure and indicate the applied torque. They offer high accuracy and can store multiple torque settings, making them ideal for applications that require frequent torque adjustments. Some advanced models even have data logging and wireless connectivity features.
Hydraulic Torque Wrench: Hydraulic torque wrenches are designed for heavy-duty applications and can apply extremely high torque values. They use a hydraulic system to generate the necessary force, making them suitable for applications such as tightening large bolts or nuts in industrial settings.
Each type of torque wrench has its advantages and is suited for specific applications. Factors such as accuracy requirements, workspace constraints, and the range of torque values needed should be considered when selecting the appropriate type of torque wrench.
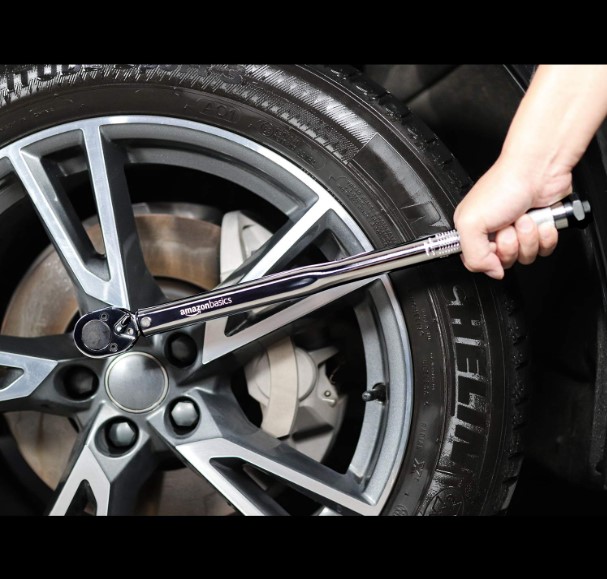
How to Use a Torque Wrench
Using a torque wrench correctly is essential to ensure proper tightening of fasteners and avoid damage. Here’s a step-by-step guide:
- Prepare the Work Area: Clear the workspace and gather all the necessary tools and components. Make sure the area is well-lit and free from distractions.
- Inspect the Torque Wrench: Check the torque wrench for any visible damage or wear. Ensure that the scale is readable and the mechanism moves smoothly.
- Set the Torque Value: Determine the required torque value for the application and adjust the torque wrench accordingly. Most torque wrenches have a dial or handle that allows you to set the desired torque value.
- Attach the Appropriate Socket or Adapter: Select the correct size socket or adapter for the fastener you’re working with and securely attach it to the torque wrench.
- Position the Torque Wrench: Place the torque wrench perpendicular to the fastener, ensuring that the handle is in a comfortable position for applying force.
- Apply Steady Pressure: Grip the torque wrench firmly and apply steady pressure in a smooth, controlled motion. Avoid jerky or sudden movements, as they can affect the accuracy of the torque measurement.
- Listen and Feel for the Click or Audible Signal: As you apply pressure, listen and feel for the distinct click or audible signal that indicates the set torque value has been reached. Stop applying force immediately after hearing or feeling the signal.
- Release the Torque Wrench: Once the signal is detected, release the pressure and allow the torque wrench to reset itself.
- Double-Check the Torque: If necessary, recheck the torque value by repeating the process to ensure the correct tightness.
- Reset the Torque Wrench: After completing the task, reset the torque wrench to its lowest setting to prevent damage to the internal mechanism.
Remember, proper technique and following the manufacturer’s instructions are crucial for accurate torque application and to extend the life of your torque wrench.
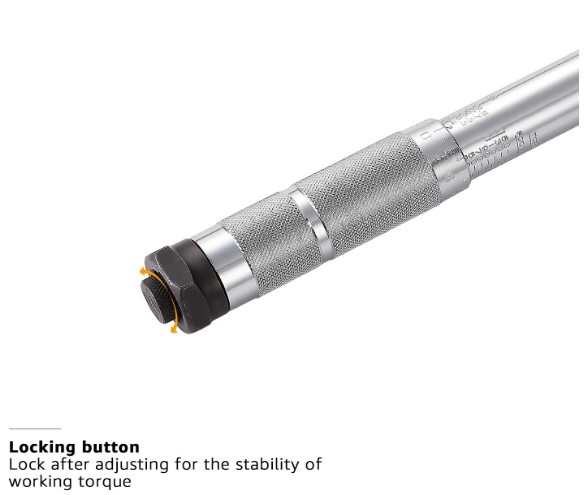
Importance of Torque Wrenches
Torque wrenches are essential tools in numerous industries, from automotive and aerospace to construction and manufacturing. These specialized wrenches are designed to apply a precise amount of torque, or rotational force, to fasteners such as nuts and bolts, ensuring they are tightened to the correct specification.
Proper torque is crucial for several reasons. First and foremost, it ensures the structural integrity and safety of the assembly. Overtightening or undertightening fasteners can lead to premature failure, potentially causing catastrophic consequences. For example, in the automotive industry, improperly torqued wheel lugs can result in a wheel separating from the vehicle while in motion, leading to a severe accident.
Additionally, torque wrenches play a vital role in maintaining the performance and efficiency of machinery and equipment. In the aerospace industry, for instance, precisely torqued fasteners are essential for the safe operation of aircraft and spacecraft. Even minor deviations in torque can lead to vibration, increased wear, and decreased fuel efficiency.
Torque wrenches are also essential in the construction industry, where they are used to ensure the proper installation of structural components, such as beams and columns. Incorrect torque can compromise the strength and stability of these structures, putting the safety of workers and occupants at risk.
Furthermore, torque wrenches are invaluable in the manufacturing sector, where they are used to assemble products ranging from automobiles to electronics. Consistent and accurate torque application is critical for maintaining product quality, reducing warranty claims, and ensuring customer satisfaction.
Failure to use torque wrenches or to apply the correct torque can have severe consequences, including equipment failure, safety hazards, and costly repairs or replacements. By using torque wrenches, professionals in various industries can ensure the proper installation and assembly of components, prolonging their lifespan, enhancing performance, and minimizing the risk of failures and accidents.
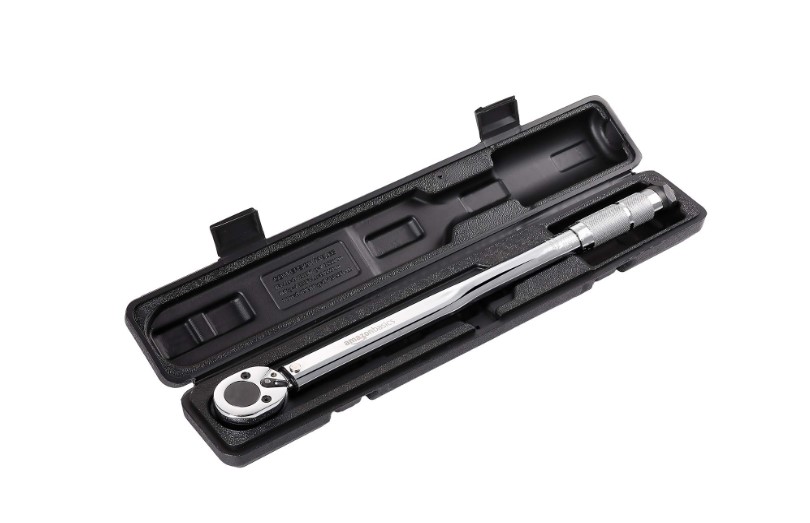
Torque Wrench Accuracy and Calibration
Torque wrenches are precision tools designed to apply a specific amount of torque to a fastener. However, their accuracy can be affected by various factors, making regular calibration essential. The accuracy of a torque wrench is crucial because over-tightening or under-tightening a fastener can lead to equipment failure, safety hazards, or premature wear and tear.
Factors Affecting Torque Wrench Accuracy
Several factors can impact the accuracy of a torque wrench:
- Wear and Tear: Over time, the internal components of a torque wrench can wear down, leading to inaccurate readings. The more a torque wrench is used, the more likely it is to experience wear and tear.
- Misuse or Abuse: Dropping, mishandling, or using a torque wrench beyond its rated capacity can damage the internal mechanisms and compromise its accuracy.
- Environmental Conditions: Extreme temperatures, humidity, and other environmental factors can affect the performance of a torque wrench, causing it to deviate from its calibrated settings.
- Manufacturing Defects: While rare, manufacturing defects can lead to inaccuracies in torque wrenches straight from the factory.
Importance of Regular Calibration
To ensure accurate and reliable performance, torque wrenches should be calibrated regularly. The frequency of calibration depends on factors such as the type of torque wrench, its usage, and the manufacturer’s recommendations. Generally, it’s recommended to calibrate torque wrenches at least once a year or after a certain number of cycles, as specified by the manufacturer.
Regular calibration helps identify and correct any deviations in the torque wrench’s readings, ensuring that it applies the correct amount of torque to fasteners. Failure to calibrate a torque wrench can lead to improper tightening, potentially causing equipment failure, safety hazards, or costly repairs.
How to Calibrate a Torque Wrench
The calibration process for torque wrenches typically involves the following steps:
- Preparation: Clean the torque wrench and ensure it is in good working condition. Follow the manufacturer’s instructions for proper preparation.
- Calibration Equipment: Use specialized calibration equipment, such as a torque tester or a calibration rig, designed specifically for torque wrench calibration.
- Testing and Adjustment: Apply various torque values to the torque wrench using the calibration equipment, and compare the readings to the known values. If the readings deviate from the expected values, adjust the torque wrench according to the manufacturer’s instructions.
- Documentation: Record the calibration results and any adjustments made to the torque wrench for future reference and traceability.
- Certification: Some industries or applications may require torque wrenches to be calibrated and certified by an accredited calibration laboratory or service provider.
Proper calibration ensures that torque wrenches maintain their accuracy and reliability, providing consistent and precise torque application for critical applications.
Torque Wrench Maintenance
Proper maintenance is crucial for ensuring the longevity and accuracy of your torque wrench. Here are some tips to keep your tool in top condition:
Storage:
- Always store your torque wrench in a clean, dry place, away from moisture, dust, and extreme temperatures.
- Consider investing in a protective case or storage box to prevent accidental damage.
- Never store a torque wrench while it’s still set to a specific torque value. Release the tension before storing it.
Cleaning:
- Regularly clean your torque wrench using a soft, lint-free cloth dampened with a mild solvent or degreaser.
- Avoid using abrasive cleaners or solvents, as they can damage the tool’s finish or internal components.
- Pay special attention to the ratchet mechanism, ensuring it’s free of debris and grime.
Lubrication:
- Lubricate the moving parts of your torque wrench according to the manufacturer’s recommendations, using the specified lubricant.
- Proper lubrication reduces friction, wear, and tear, ensuring smooth operation and prolonging the tool’s lifespan.
Calibration:
- Torque wrenches should be calibrated periodically to maintain their accuracy. The frequency of calibration depends on usage and the manufacturer’s guidelines.
- Consider sending your torque wrench to an authorized service center or calibration lab for professional calibration.
Handling:
- Treat your torque wrench with care, avoiding dropping, striking, or subjecting it to excessive force.
- Never use a torque wrench as a breaker bar or for any purpose other than its intended use.
- Inspect the tool regularly for signs of wear, cracks, or damage, and replace it if necessary.
By following these maintenance tips, you can ensure that your torque wrench remains accurate, reliable, and ready for use whenever you need it.
Selecting the Right Torque Wrench
Choosing the appropriate torque wrench is crucial for ensuring accurate and consistent torque application, preventing over-tightening or under-tightening, and maintaining the integrity of the fasteners and components. Several factors should be considered when selecting a torque wrench:
Torque Range: Torque wrenches are designed to operate within specific torque ranges, typically measured in foot-pounds (ft-lbs) or newton-meters (N-m). It’s essential to select a wrench with a torque range that encompasses the required torque values for your application. Using a wrench outside its intended range can lead to inaccurate readings and potential damage.
Drive Size: Torque wrenches are available with different drive sizes, such as 1/4 inch, 3/8 inch, 1/2 inch, and 3/4 inch. The drive size should match the size of the sockets or attachments you’ll be using. Choosing the wrong drive size can result in improper fit, potential damage, and inaccurate torque application.
Application Requirements: Different industries and applications have specific torque requirements and standards. For example, automotive repairs may require different torque values than industrial machinery maintenance. Consider the specific application and any industry-specific guidelines or regulations when selecting a torque wrench.
Type of Torque Wrench: Torque wrenches come in various types, such as beam-style, dial-type, and click-type. Each type has its advantages and limitations in terms of accuracy, ease of use, and durability. Choose the type that best suits your needs and preferences.
Measurement Units: Torque wrenches can display measurements in different units, such as foot-pounds (ft-lbs), inch-pounds (in-lbs), or newton-meters (N-m). Select a wrench that displays the units you’re most comfortable working with or that are required by your specific application.
Ergonomics and Comfort: Consider the ergonomics and comfort of the torque wrench, especially if you’ll be using it frequently or for extended periods. Look for features like non-slip grip, comfortable handle design, and easy-to-read displays to reduce fatigue and improve accuracy.
Brand and Quality: Reputable brands with a proven track record of producing high-quality torque wrenches are generally more reliable and accurate. While cost should be considered, it’s essential to prioritize quality and accuracy, as a faulty torque wrench can lead to costly mistakes and potential safety issues.
By carefully considering these factors, you can select the right torque wrench for your specific application, ensuring accurate and consistent torque application, prolonging the life of your tools and components, and maintaining a safe working environment.
Torque Wrench Safety
Using a torque wrench improperly can lead to serious injuries and damage. It’s crucial to follow safety precautions and best practices to ensure your well-being and the integrity of the equipment you’re working on.
First and foremost, always wear appropriate personal protective equipment (PPE) when using a torque wrench. This includes safety glasses to protect your eyes from flying debris, gloves to improve grip and protect your hands, and steel-toed boots to safeguard your feet.
Before using a torque wrench, inspect it for any signs of damage or wear. Check for cracks, dents, or other visible defects that could compromise its performance and accuracy. Additionally, ensure that the torque wrench is properly calibrated and within its recommended calibration interval.
When tightening or loosening fasteners, always position yourself in a stable and balanced stance. Avoid awkward or compromised body positions that could cause you to lose control or strain your muscles. If working in a confined space, be mindful of your surroundings and potential pinch points.
Never use a torque wrench as a breaker bar or attempt to loosen seized fasteners with it. Doing so can damage the torque wrench and potentially cause it to break, leading to injuries. Instead, use appropriate tools, such as impact wrenches or penetrating lubricants, to break loose stubborn fasteners before switching to the torque wrench.
When tightening or loosening fasteners, apply smooth and controlled movements. Avoid jerky or sudden motions that could cause the torque wrench to slip or create excessive torque spikes, potentially damaging the equipment or causing injuries.
Finally, store and transport torque wrenches properly to prevent damage. Use designated storage cases or containers, and avoid exposing them to excessive moisture, heat, or other environmental factors that could affect their accuracy and performance.
By following these safety precautions and best practices, you can minimize the risks associated with using torque wrenches and ensure a safe and effective working environment.
Common Torque Wrench Mistakes
One of the most common mistakes when using a torque wrench is failing to reset it properly after each use. Many torque wrenches have a mechanism that needs to be reset or “zeroed out” before applying torque to a new fastener. Neglecting to reset the wrench can lead to inaccurate torque readings and potentially over-tightening or under-tightening the fastener.
Another frequent error is using the wrong type of torque wrench for the application. Torque wrenches are designed for specific torque ranges and drive sizes. Using a wrench that is not rated for the required torque value or drive size can compromise accuracy and potentially damage the wrench or the fastener.
Improper technique when using a torque wrench is also a common issue. It’s essential to apply force perpendicular to the wrench handle and avoid side-loading or jerking motions, which can skew the torque reading. Additionally, some torque wrenches require a specific “pull” or “push” motion, and using the wrong technique can affect accuracy.
Failing to maintain and calibrate the torque wrench regularly is another mistake that can lead to inaccurate torque readings. Torque wrenches are precision instruments and can become less accurate over time due to wear and tear. Regular calibration and maintenance by a qualified professional are crucial to ensure the wrench’s continued accuracy.
Finally, using a damaged or worn torque wrench is a common error that should be avoided. Any visible signs of damage, such as cracks, dents, or worn components, can compromise the wrench’s accuracy and potentially lead to safety hazards. It’s essential to inspect the torque wrench before each use and replace it if any damage is detected.
To avoid these common mistakes, it’s crucial to read and follow the manufacturer’s instructions carefully, select the appropriate torque wrench for the job, use proper technique, maintain and calibrate the wrench regularly, and promptly replace any damaged or worn components.
Torque Wrench Innovations and Future
Torque wrench technology has seen significant advancements in recent years, driven by the demand for greater accuracy, efficiency, and user-friendliness. One of the most notable innovations is the introduction of digital torque wrenches, which use electronic sensors and displays to provide precise torque measurements. These wrenches eliminate the need for manual adjustments and offer increased accuracy and consistency.
Another innovation is the development of wireless torque wrenches, which can communicate with smartphones or other devices via Bluetooth or Wi-Fi. This technology allows for real-time data monitoring, recording, and analysis, enabling better quality control and traceability in various applications.
Advancements in materials and manufacturing processes have also led to the creation of lighter and more durable torque wrenches. The use of advanced alloys and composite materials has resulted in tools that are more resistant to wear and tear, while still maintaining their precision and accuracy.
Looking to the future, the integration of artificial intelligence (AI) and machine learning (ML) technologies into torque wrench design and operation is a promising area of development. AI-powered torque wrenches could potentially self-calibrate, predict maintenance needs, and even suggest optimal torque settings based on environmental conditions and application requirements.
Additionally, the adoption of Internet of Things (IoT) technology in torque wrenches could enable remote monitoring and control, allowing for real-time data sharing and analysis across multiple locations or job sites. This could lead to improved efficiency, productivity, and quality control in various industries.
As the demand for precision and efficiency continues to grow, the torque wrench industry is likely to witness further innovations that will enhance user experience, increase accuracy, and improve overall tool performance.